What is MTBF?
Mean Time Between Failures (MTBF) is a statistical measure of the average time period between failures for a system or product. It is used as a reliability metric to predict the expected operational time for a system without failure. MTBF is calculated by dividing the total operating time of a system by the number of failures that occurred during that time period.
MTBF is calculated by dividing the total number of hours by all products within a given product line by the number of failures in those same products.
For example: If you have 500 units in your product line, they collectively run for 10 million hours before one fails; therefore your MTBF would be 10 million divided by 500 = 20 thousand hours per unit.
What is MTTR?
Mean Time Between Repairs (MTBR) is a metric that measures the average time between repairs or maintenance activities for a system or product. It is a measure of the reliability and availability of a system, and it is calculated by dividing the total operating time of a system by the number of repair or maintenance events that occurred during that time period. A higher MTBR value indicates that a system is more reliable and requires less frequent repairs.
Let's say we have a manufacturing machine that operates for 1000 hours in a year and experiences 3 repair events during that time. The total time spent on repairs for all three events is 12 hours. To calculate MTBR, we divide the total operating time (1000 hours) by the number of repair events (3):
MTBR = 1000 hours / 3 repair events = 333.33 hours
This means that the machine experiences an average of 333.33 hours of operation time between each repair event. A higher MTBR value would indicate that the machine is more reliable and requires less frequent maintenance. On the other hand, a lower MTBR value would indicate that the machine is less reliable and requires more frequent maintenance.
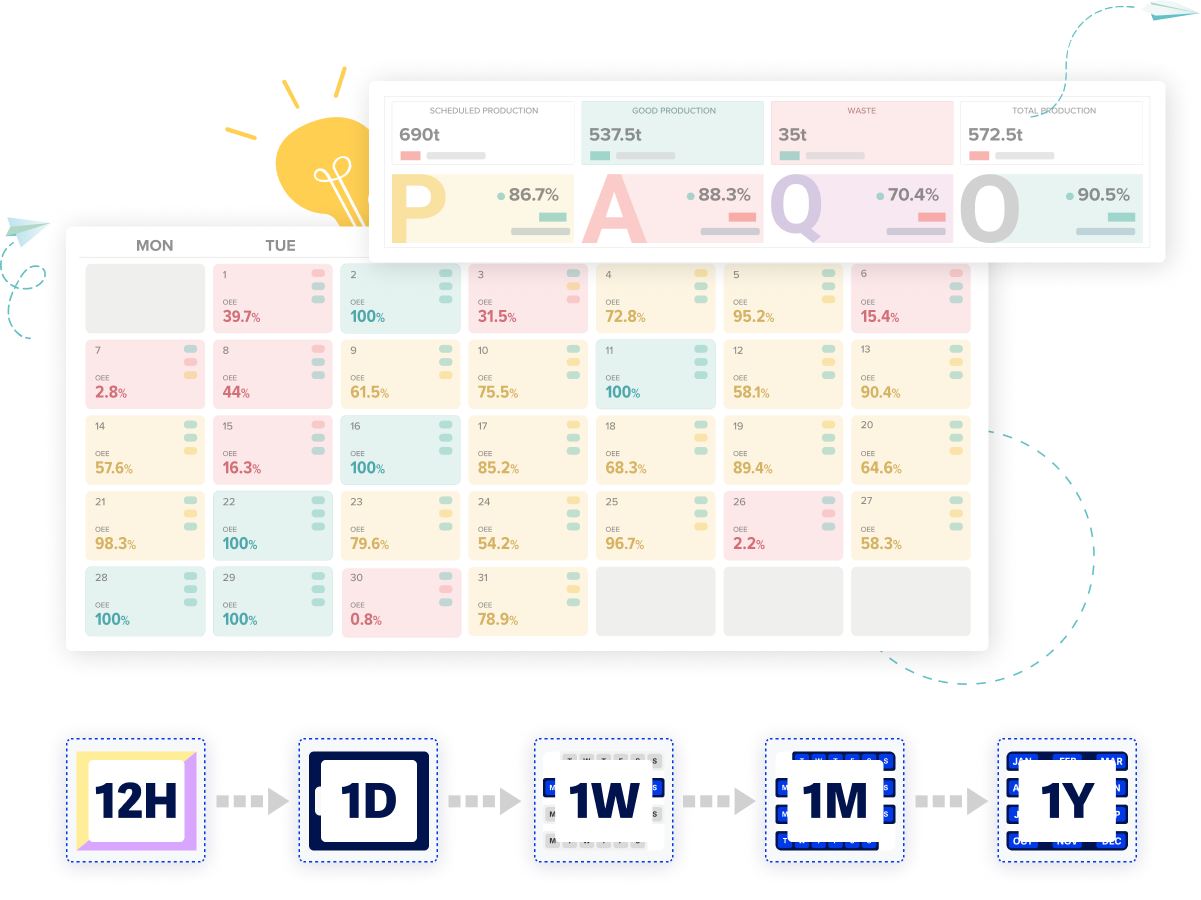
Plan maintenance anytime quickly
Benefits to Operations Management
MTBF and MTBR are important performance metrics for operations managers. They can be used to improve efficiency and reduce costs, as well as help operations managers make data-driven decisions.
The benefits of MTBF and MTBR to operations management are:
- MTBF (Mean Time Between Failures) helps to predict the reliability of a system and the expected operational time without failure. This information can be used by operations managers to plan for maintenance and support activities, allocate resources, and manage the replacement of parts.
- MTBR (Mean Time Between Repair) helps to evaluate the efficiency of the maintenance and support process. Operations managers can use MTBR to monitor the performance of their maintenance teams, identify areas for improvement, and make informed decisions about maintenance schedules and resource allocation.
- Both MTBF and MTBR provide valuable insights into the performance and reliability of systems and products. This information can be used to improve the quality of products, reduce costs, and enhance customer satisfaction.
- MTBF and MTBR can also be used to compare different systems or products and make informed decisions about investments in new technology or equipment./li>
Achieving a High MTBF or MTBR Rate
Here are some steps that can be taken to achieve a high MTBF or MTBR rate:
- Implement preventive maintenance: Regularly scheduled preventive maintenance can help to identify and resolve potential problems before they lead to a failure.
- Use high-quality components and materials: Using high-quality components and materials can increase the reliability and durability of a system, reducing the likelihood of failure.
- Improve design and manufacturing processes: Improving design and manufacturing processes can help to eliminate defects and reduce the occurrence of failures.
- Train personnel: Proper training of personnel can help to ensure that maintenance and repair activities are performed correctly and efficiently, reducing the time required for repairs.
- Monitor performance: Regular monitoring of system performance can help to identify trends and potential problems, allowing for proactive interventions to improve reliability.
- Invest in technology: Investing in technology, such as predictive maintenance systems, can help to identify potential failures before they occur and improve the efficiency of the maintenance and repair process.
Improve your maintenance planning and optimize the entire process
With cutting-edge MES solutions, you can improve your maintenance planning and optimize the entire process. With this type of software, you'll be able to:
- Improve equipment uptime, which means more production and increased profitability.
- Streamline maintenance planning by automatically detecting faults and suggesting preventive maintenance steps that may help to prevent breakdowns in the future. This allows for better maintenance planning with less downtime at a lower cost per hour worked on each piece of equipment because operators do not need extensive training before using it for the first time.
- Increase profitability by reducing supply chain costs and increasing production rates. Improve quality control by tracking the entire process from start to finish, which helps you identify areas where improvements can be made. This will help you avoid costly mistakes and improve your reputation as a manufacturer.
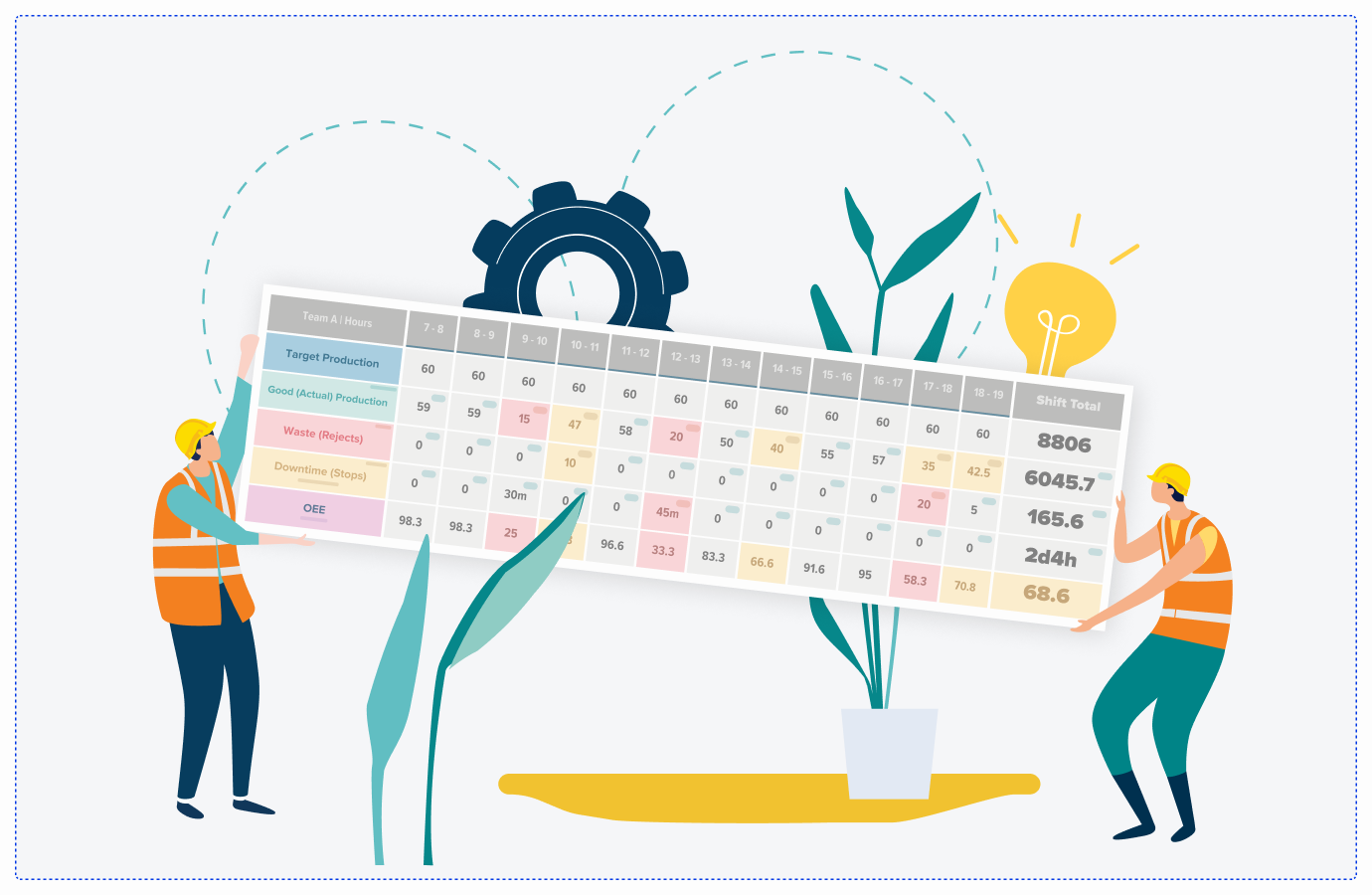
Create maintenance plan anytime with MES
Conclusion
We hope this article has helped you to understand the importance of MTBF and MTBR in operations management. As a operation manager, it's vital that you know how to apply these metrics so that they can be used as tools for improving performance and making better decisions.